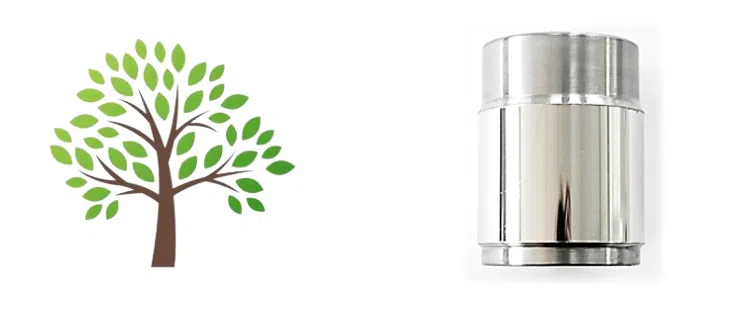
METALTEK® is a thermal spray coating produced using the HP HVOF process.
This coating is applied to cylindrical parts to provide abrasion and corrosion resistance in moderately corrosive industrial environments.
The coating’s mechanical properties and density guarantee excellent sliding properties, resistance to mechanical wear and chemical corrosion.
These parameters contribute to a significant improvement in the service life of coated parts.
METALTEK® is the result of a combination of materials, process and parameters.
With its 30 years of experience, Douce-Hydro has developed the machine’s parameters and settings to optimize the final results.
The process is subject to maximum control thanks to the qualifications and internal controls carried out.
The powders themselves are subject to special controls, monitoring and traceability.
The high-pressure, high-velocity Oxygen-Fuel mixture(HP HVOF) thermal spraying process involves melting various powders in a mixture of fuel and oxygen accelerated by a special torch.
Depending on how the powder is injected, it can be projected at extremely high speeds of up to 1,100 m / s.
And, depending on the fuel selected, the flame temperature can reach 4 , 000°C, so the sprayed powders are melted with optimum homogeneity.
The resulting coatings feature zero porosity and higher bond strength than the first-generation HVOF system.
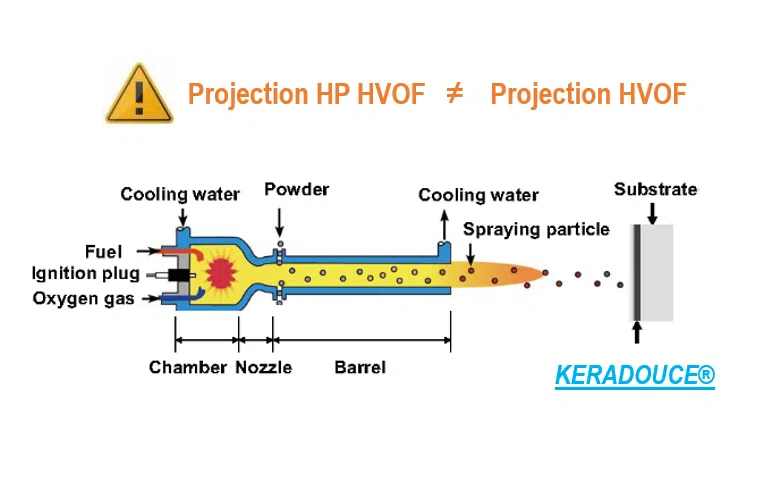
Complete internal process
- Continuous improvement of processes, operations and tooling.
- Total control of production time and inventory management
- No extra costs or delays due to deliveries from subcontractors during manufacturing.
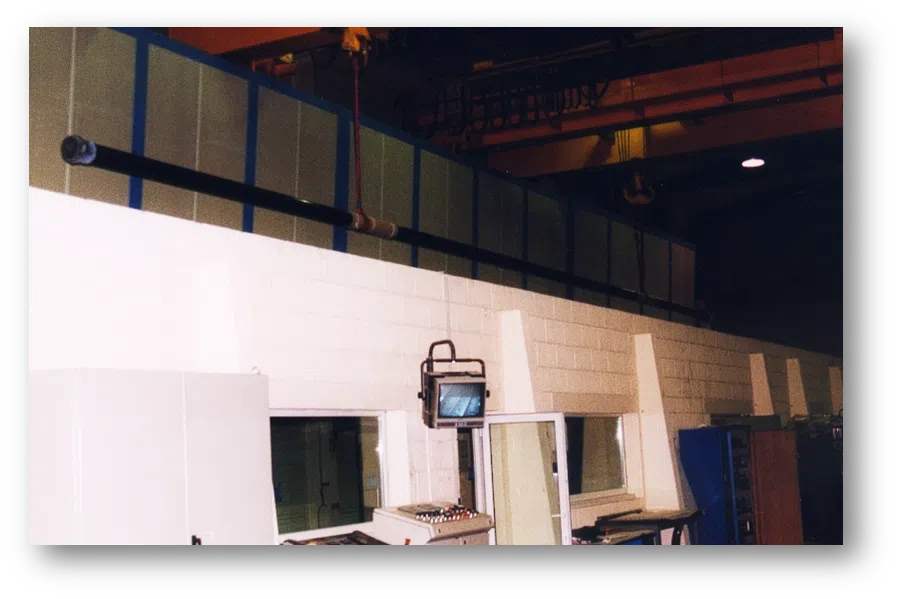
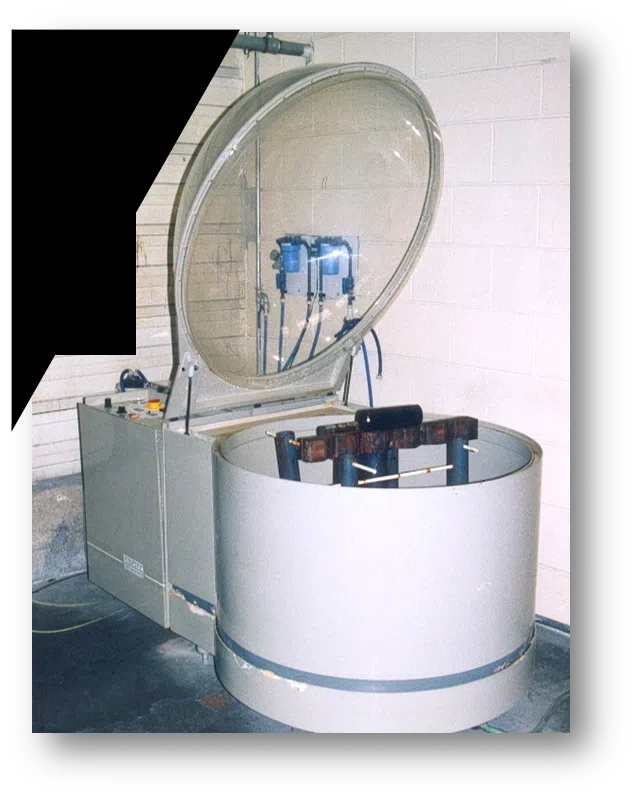
Acetic Salt Spray Test Equipment
This test is carried out in accordance with NF ISO 9227 (ASTM B 287) .
Enclosure: cylindric of 1000 l (ERICHSEN Model 606 – 1000L)
Features of the salt solution :
- [NaCl] = 5% in demineralized water.
- pH = 3.2 ± 0.1 added with CH3COOH.
- rainfall: 1.5 ± 0.1 ml/h/80 cm².
- Density = 1.035 ± 0.005.
- Temperature: 35°C ± 2°C.
- Air pressure: 1 bar ± 0.2 bar (= 14.5 psi ± 2.9 psi)
- Sample position: placed horizontally on two plastic bars.
- Sample preparation: ends protected with grease and coating degreased with acetone.
The test stops when a trace of corrosion appears; the duration of the test is read on the counter.
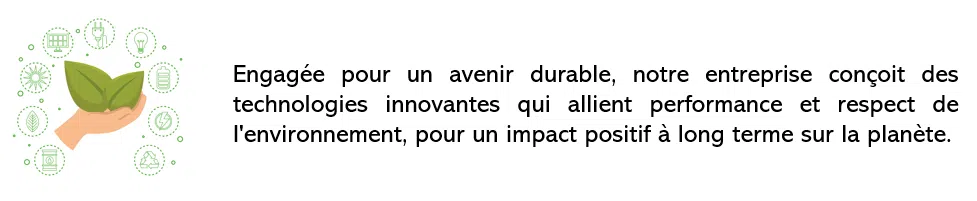